Vicinity Reviews & Pricing
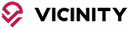
What is Vicinity?
Industry Specialties: Colleges and universities, Commercial real estate, Government, Healthcare, Hospitality, Industrial and manufacturing, Life sciences, Residential real estate.
Vicinity Software offers a comprehensive solution for managing manufacturing tasks, specifically tailored for process manufacturers. This software excels in handling complex production processes, including batch ticket management, formula management, and quality control. It is particularly well-suited for industries such as food and beverage, chemical, and cosmetics manufacturing, where precise formulation and stringent quality standards are critical.
One of the standout benefits of Vicinity is its ability to integrate seamlessly with existing ERP systems, enhancing overall operational efficiency. Users appreciate its robust features like real-time inventory tracking, detailed production scheduling, and comprehensive reporting capabilities. These features empower manufacturers to optimize their production workflows, reduce waste, and ensure compliance with industry regulations.
Compared to similar products, Vicinity is often praised for its user-friendly interface and the depth of its industry-specific functionalities. While specific pricing details are not readily available, potential users are encouraged to contact SelectHub for a tailored pricing quote based on their unique requirements.
Vicinity Pricing
Based on our most recent analysis, Vicinity pricing starts in the range of $100 - $500.
- Price
- $$$$$
- Starting From
- Undisclosed
- Pricing Model
- Monthly, Quote-based
- Free Trial
- No
Training Resources
Vicinity is supported with the following types of training:
- Documentation
- In Person
- Live Online
- Videos
- Webinars
Support
The following support services are available for Vicinity:
- Phone
- Chat
- FAQ
- Forum
- Help Desk
- Knowledge Base
- Tickets
- Training
- 24/7 Live Support
Vicinity Benefits and Insights
Key differentiators & advantages of Vicinity
- Improved Production Efficiency: Streamline manufacturing processes by automating routine tasks, reducing manual errors, and optimizing resource allocation.
- Enhanced Inventory Management: Maintain optimal stock levels with real-time tracking and automated reordering, minimizing both overstock and stockouts.
- Cost Reduction: Identify and eliminate waste in production processes, leading to significant cost savings and higher profit margins.
- Better Quality Control: Implement stringent quality checks at various stages of production, ensuring consistent product quality and reducing defects.
- Data-Driven Decision Making: Leverage comprehensive analytics and reporting tools to make informed decisions based on real-time data and historical trends.
- Regulatory Compliance: Ensure adherence to industry standards and regulations with built-in compliance features, reducing the risk of legal issues and fines.
- Scalability: Easily scale operations up or down to meet changing market demands without significant disruptions or additional costs.
- Enhanced Collaboration: Foster better communication and collaboration among different departments, leading to more cohesive and efficient operations.
- Customer Satisfaction: Improve delivery times and product quality, resulting in higher customer satisfaction and loyalty.
- Resource Optimization: Maximize the utilization of machinery, labor, and materials, ensuring that resources are used efficiently and effectively.
- Reduced Downtime: Predict and prevent equipment failures with proactive maintenance scheduling, minimizing production interruptions.
- Environmental Sustainability: Implement eco-friendly practices by reducing waste and energy consumption, contributing to corporate social responsibility goals.
- Customizable Workflows: Tailor the software to fit specific business needs and workflows, enhancing overall operational flexibility.
- Real-Time Monitoring: Gain instant visibility into production status and performance metrics, enabling quick responses to any issues that arise.
- Integration Capabilities: Seamlessly integrate with existing ERP, CRM, and other business systems, ensuring a unified and efficient operational ecosystem.
Industry Expertise
Vicinity Reviews
Based on our most recent analysis, Vicinity reviews indicate a 'great' User Satisfaction Rating of 86% based on 6 user reviews from 2 recognized software review sites.
Synopsis of User Ratings and Reviews
Based on an aggregate of Vicinity reviews taken from the sources above, the following pros & cons have been curated by a SelectHub Market Analyst.
Pros
Cons
Researcher's Summary:
How can Vicinity help your business manufacture success? User reviews from the past year highlight Vicinity's strengths in inventory management, with users praising its ability to effectively allocate and track inventory, which is essential for batch manufacturers dealing with complex recipes and ingredients. The software's customizable interface also receives positive feedback, allowing users to tailor views and connect related information, simplifying complex processes. However, some users find the onboarding process and initial setup to be challenging, suggesting a steeper learning curve for those unfamiliar with similar systems.
What truly differentiates Vicinity is its industry-specific focus. The software offers tailored solutions like VicinityFood and VicinityChem, catering to the unique needs of food, chemical, and brewery manufacturers. This specialization is crucial for businesses in these sectors, as it addresses their specific regulatory requirements and production workflows. While the initial learning curve might seem daunting, Vicinity's focus on continuous development based on customer feedback demonstrates its commitment to improvement and user satisfaction.
In conclusion, Vicinity is best suited for batch and process manufacturers, particularly in the food, chemical, and brewery industries, who require robust inventory management, customizable workflows, and industry-specific features. Its strengths lie in its specialized solutions and continuous improvement, making it a valuable asset for businesses looking to streamline production and maintain quality control.
Key Features
- Bill of Materials (BOM) Management: Efficiently manage complex BOMs with multi-level hierarchies and detailed component tracking.
- Formula Management: Maintain precise control over formulations, including version control and ingredient substitutions.
- Production Scheduling: Optimize production schedules with real-time adjustments and resource allocation.
- Quality Control: Implement rigorous quality checks at various stages of production to ensure compliance with industry standards.
- Lot Tracking: Track raw materials and finished goods by lot number for enhanced traceability and recall management.
- Costing Analysis: Perform detailed cost analysis to understand the financial impact of production decisions.
- Inventory Management: Monitor inventory levels in real-time to prevent stockouts and overstock situations.
- Compliance Management: Ensure adherence to regulatory requirements with built-in compliance tracking and reporting tools.
- Reporting and Analytics: Generate comprehensive reports and analytics to gain insights into production efficiency and performance.
- Integration Capabilities: Seamlessly integrate with other enterprise systems such as ERP and CRM for a unified data environment.
- Scalability: Adapt to growing business needs with scalable architecture that supports expansion and increased production volumes.
- User-Friendly Interface: Navigate the system with ease thanks to an intuitive and user-friendly interface.
- Customizable Workflows: Tailor workflows to match specific business processes and operational requirements.
- Real-Time Data Access: Access up-to-date information across the production lifecycle for informed decision-making.
- Supplier Management: Manage supplier relationships and performance with integrated supplier management tools.